FAQ
Glossary of ESD Terms
Air ionizer: a device that produces large quantities of both positive and negative ions. These air molecules are directed in areas where electrostatically charged objects require neutralization.
Antistatic: an obsolete term often used generically to describe the full range of static control materials and products. This term has been misused and misapplied, resulting in a great deal of confusion between suppliers and end users. A new term, “low charging,” has replaced the word antistatic.
Catastrophic failure: a device that completely ceases to function. It is usually the result of some type of electrical, thermal or mechanical overstress.
Charge device model (CDM): a failure model where the part in question holds an electrostatic charge and rapidly discharges to another object when they are brought into contact. The discharge could cause a device failure.
Conductive material: an ESD protective material having a surface resistivity of 105 ohms per square centimeter (ohms/cm2). If configured correctly, conductive material provides static event shielding.
Degradation: a type of static electricity damage that weaken an electronic device but still allows it to continue to operate within normal parameters. However, a degraded device may later fail catastrophically.
Dissipative material: An ESD protective material having a surface resistivity greater than 105ohms/cm2, but less than 1012 ohms/cm2.
Electrostatic charge: the type of electrical energy generated during tribocharging. The amount of charge created depends upon the amount of friction generated during contact separation. Other factors include relative humidity, speed of separation and properties of the materials involved.
Electrostatic discharge (ESD): the usually sudden transfer of voltage between bodies at different voltage potentials.
Failure model: several different models have been developed to identify the way an ESD event can damage or destroy a device. The three most common failure models are the charge device model (CDM), the human body model (HBM) and the machine model (MM).
Foot strap: a special device that relies on electrical contact between the user’s shoe and a conductive flooring system to limit electrostatic buildup on the wearer.
Ground: a conducting connection, whether intentional or accidental, between an electrical circuit or equipment and the earth, or to some conducting body that serves in place of earth. The mass is capable of supplying or accepting a large electrical charge.
Grounding: the process of establishing a connection between an electrical circuit or equipment and an earth ground or electrical ground.
Human body model (HBM): people are a primary source of ESD and are often responsible for part damage. Because the human body has a charge-storage capacitance and a highly conductive sweat layer, the discharge from a person’s touch can be simulated using a resistor-capacitor circuit.
Inductance: an energy phenomenon that occurs as an electric field changes strength or polarity. During this transition, changes in the field can cause an electrical current to flow in a nearby object.
Inductive charging: a process in which an electrically floating (i.e., not grounded) object or surface is subjected to an electrostatic field. The exposed object will then acquire an electrostatic charge as a result of this exposure.
Insulative material: a material having a surface resistivity greater than 1012 ohms/cm2.
Ion: a charged particle, usually of air or nitrogen. The charge can either be positive (+) or negative (-). A positive charge is the result of missing electrons. A negative charge is the result of extra electrons.
Ionization: a device that is used where effective grounding cannot be employed to bleed off static charges, such as a charged insulator. Ion generation is usually accomplished using a high-voltage emitter system.
Latent failure: a device failure that does not occur immediately at the time of overstress. Latent defects are very difficult to measure and usually shorten the life span of a part.
Low charging: refers to the low static charge generation between surfaces that contact and separate. This term has replaced the word “antistatic.”
Machine model (MM): an ESD test that simulates automatic handling operations. It is based on a discharge network consisting of a charged 200 picofarad capacitor and (nominally) 0 ohms of series resistance.
Neutralization: the process of eliminating potentially harmful static charges by exposing a charged object to ionized air. The static charges on the surface attract opposite charged ions from the air so that the ions recombine to reform neutral molecules.
Relative humidity: humid air contains moisture that helps dissipate electrostatic charges and reduce charge buildup by increasing surface conductivity. High relative humidity will reduce charge formation but will not prevent static charge buildup or discharge.
Shielding: an electrostatic field radiates in the area surrounding most charged objects. This field can produce an ESD event or inductively charge other objects nearby and produce undesirable results. A conductive, grounded enclosure, such as a Faraday cage, that completely surrounds an object will shield the contents within from the effects of an external electrostatic field. A metallized bag or a conductive tote box are examples of shielding.
Static dissipative material: a material that allows electrons to flow across its surface or through its mass. It is more resistive than conductive material and less resistive than insulative or nonconductive material.
Static electricity: an electrical charge caused by an imbalance of electrons on the surface of a material.
Triboelectric charging: the generation of static electricity that results from two materials coming into contact and then separating. When this phenomenon occurs, one of the materials typically comes away with a positive charge; the other receives a negative charge. Tribo comes from the Latin word meaning “to rub.”
Wrist strap: a special device that forms an electrical connection between the user and a ground. It is designed to limit the buildup of electrostatic voltage on the wearer’s skin. Wrist straps usually consist of a conductive bracelet and some type of tether wire with a built-in safety resistance.
Zap: the mild electrical shock a person may feel when he has built up a charge of at least 3,000 volts on his body and then discharges by touching a grounded object at a different electrical potential, causing electrons to transfer suddenly.
Common ESD Questions
Why worry about ESD?
ESD can cause unseen damage to electronic components during manufacture of electronic assemblies and equipment. If the damaged component fails immediately, the result can be a board that fail tests and requires rework. This represents lost production and additional manufacturing costs.
Worse than this, a component may be partially damaged and weakened. It may suffer a change or drift in characteristics. It may remain within specification, but fail later when in use by a customer. It has been estimated that 90% of damaged devices may be discovered in this way. This is the most expensive type of failure, as it represents:
- Customer dissatisfaction, and the possibility of loss of product reputation and future sales
- Customer service personnel and facility cost
- Engineers time, possibly for on-site repair with travel, and parts replacement
Analysis of non-conforming or defective devices showed that 60-75% were damaged by EOS (electrical overstress) or ESD. This rises to 90% for newer technologies. About 70% of these failures were attributed to damage from incorrectly grounded people.
In manual assembly most ESD arises from charged personnel, if they are not grounded.
Most people do not feel an ESD shock unless they are charged to over 4000 V (the sensitivity threshold varies between people, and even over parts of the body!). This voltage is quite common in the uncontrolled environment – how many of us have not felt the occasional electrostatic shock in everyday life?
What is an EPA or Electrostatic PrArea?ve Area ?
Prevention of ESD bases on Electrostatic Protective Area (EPA). EPA can be a small working station or a large manufacturing area. The main principle of an EPA is that there are no highly charging materials in the vicinity of ESD sensitive electronics, all conductive materials are grounded, workers are grounded, and charge build-up on ESD sensitive electronics is prevented. International standards are used to define typical EPA and can be found for example from International Electrotechnical Commission (IEC) or American National Standards Institute (ANSI).
ESD prevention within an EPA may include using appropriate ESD-safe packing material, the use of conductive filaments on garments worn by assembly workers, conducting wrist straps and foot-straps to prevent high voltages from accumulating on workers’ bodies, anti-static mats or conductive flooring materials to conduct harmful electric charges away from the work area, and humidity control. Humid conditions prevent electrostatic charge generation because the thin layer of moisture that accumulates on most surfaces serves to dissipate electric charges.
I usually wear one foot grounder, but have been told to wear two, one on each foot. Why?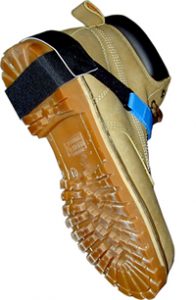
The foot grounder only works properly when worn correctly and in conjunction with a conductive or dissipative floor. The act of walking is a perfect example of triboelectric generation. If your properly worn foot grounder is in contact with an ESD floor, then all charges on your body (skin) are drained to ground so the net difference (voltage) between you and ground is zero. But, as soon as that foot with the foot grounder is lifted into the air, your body becomes charged again, either through induction from your clothing or triboelectric generation from the contact and separation of your foot (feet). If you were to wear two foot grounders, one on each foot, then you further minimize the chance you have of holding a net charge much greater than a few volts (typically 2,000 – 5,000 Volts) because you are increasing your time in a grounded state. We recommend wearing a foot grounder on each foot or a pair of ESD shoes when you go mobile.
If a mat and the wrist strap are connected together, do they need to be connected to earth (ground) potential?
No, but the equipment being worked on should be both unplugged and electrically connected to the ESD mat. As long as all conductive parts, (body’s skin, ESD mat, equipment chassis, parts being handled, etc.), are at the same potential, there will be no opportunity for an ESD event (discharge). Earth ground happens to be a very convenient reference voltage to connect to. If you ensure that all conductive parts are tied to earth ground, then you meet the same requirement that they are at the same potential. It is when you have a difference in the potential (voltage or net charge) between two conductors that, (either touch together or come in near proximity), will lead to a discharge (ESD event).
Are wrist straps necessary if all other ESD precautions are taken (i.e., two ground [foot] straps, jacket, dissipative flooring, grounded mats
, etc.)? If so, why?
Wrist straps are not necessary if an operator is wearing two foot grounders on a conductive grounded floor and doesn’t lift both heels/toes at the same time, like some people do when sitting down. If an operator is also wearing a esd jacket, but is not electrically connecting the jacket to either their body’s skin or ground, then the jacket is providing only partial protection. Charges on the jacket may have no where to go or discharge to if the jacket is not grounded. A popular way to ground the jacket is with a coil cord either attached to a snap on the waist area of the jacket or via a wrist strap snapped to the inside cuff of an ESD jacket. Our wrist strap WB2500 can be used with most industry standard jackets with this feature.
We are setting up work stations for handling static sensitive devices. What are some guidelines we should follow to be sure we are adequately protecting our components?
An ESD protective workstation refers to the work area of a single individual that is constructed and equipped with materials and equipment to limit damage to ESD sensitive items. It may be a stand-alone station in a stockroom, warehouse, or assembly area, or in a field location such as a computer bay in commercial aircraft. A workstation also may be located in a controlled area such as a clean room. The basic concept of the ESD protective workstation is to keep all materials and personnel at the same electrical potential. Electrostatic discharge occurs when two objects at different potentials come into contact with or in the proximity of each other. If the potentials are equal, no discharge occurs. The key ESD control elements comprising most workstations are a static dissipative work surface, a means of grounding personnel (usually a wrist strap), a common grounding connection, and appropriate signage and labeling.
Some of our ESD benches have the wrist strap going directly to ground and others to a work bench ESD mat which (on the opposite corner) then goes through a common point ground cord with a resistor to ground. Which is right?
Neither are necessarily correct because of the dependency on the relationship of the wrist strap that is directly grounded and the potential of the workbench mat. The concept of grounding at an ESD safe bench is to bring to the same potential all conductors, thus minimizing the possibility of a potential difference between two conductors or its resultant discharge. Power ground or earth ground happens to be a convenient potential to connect into because it is consistent within the controlled environment. If both the wrist strap and the ESD mat are connected to the same point at ground, then they have the same potential and are properly setup. The wrist strap that connects first to the ESD mat, second through the mat, third from the opposite corner of the mat and fourth to ground has the addition of the serial impedance of the mat (resistance and capacitance) to ground to contend with. At times the operator may be at a different potential than grounded bench equipment or ESD sensitive devices on the mat.
How well does relative humidity of the surrounding atmosphere control the ESD?
The relative humidity (RH) directly affects the ability of a surface to store surface charges. The higher the RH, the less time an item will hold a charge. The method of surface charge reduction [due to increased RH] can be attributed to recombination and or conduction. As the RH increases, so does the natural conductivity of the air, but even at 100% RH the increase in the natural discharge rate cannot be substituted for proper ESD control practices.
We have a conductive floor in our plant that gives readings less than 1.0 x 105 when I test it. Is this a safety concern?
I know that the readings shouldn’t go above 1.0 x 109, but is there a lower limit? What documentation will back this up? We have been using a dissipative wax on the floor and the readings are consistently between 1 x 105 and 1 x 109; however, we would like to discontinue this practice to save money.
Lower limits of floor to ground resistance are a matter of company or local electrical codes. Some areas allow as low as 1x10E4 ohms to ground and some areas require no lower than 1 x 10E6 ohms to ground. A common value is at 1 x 10E5 ohms to ground. If the resistance to ground values vary in an area, then it is wise to create a “map” that shows the “hot spots” where it might be wise to treat them with something to raise the resistance to within the acceptable range based on the maximum current exposure people should experience (using Ohms Law – E=IR).
What is the difference between antistatic, conductive and static dissipative?
The terms conductive and static dissipative typically refer to resistance or resistivity ranges used in the evaluation of ESD control materials and products. By definition, a conductive material has a surface resistivity of less than 1 x 10E5 ohms per square or a volume resistivity less than 1 x 10E4 ohm-cm. A static dissipative material has a surface resistivity of 1 x 10E5 to 1 x 10E12 ohms per square or a volume resistivity of 1 x 10E4 to 1 x 10E11 ohm-cm. These definitions appear in the ESD Association Glossary as well as in various other static control standards documents. For some materials, surface resistance rather than surface resistivity is often used to define these terms. In this case, a simple conversion factor is applied, dividing the resistivity ranges by 10. Thus conductive becomes less than 1 x 10E4 ohms and static dissipative becomes 1 x 10E4 to 1 x 10E11 ohms, provided that the appropriate electrodes with the correct geometric conversions are used. ANSI/ESD S11.11 provides additional information on this issue. The term antistatic, however, does not refer to resistance or resistivity. By definition, the term refers to a material that resists tribocharging. At one time, the term referenced a resistance value, but it was severely misused and today no longer represents any resistance range.
Are there any problems using cell phones near ESD devices or assemblies?
Some investigators in the disk drive area have found that under certain test conditions that GMR heads can be altered or damaged if near an activated cell phone. The testing was contrived a bit in that a large coaxial antenna was attached across the magnetic stripe of the GMR head and the cell phone operated within inches of the antenna. Naturally, this sort of condition should not occur in actual practice but it does show that the sensitivity of the particular item was quite high (easy to damage). Of course a charged piece of plastic waved in front of the antenna would have resulted in the same problem or worse. The signal strength of a cell phone should not cause problems to anything of a practical nature. Have a look at papers presented in the EOS/ESD Symposia from 1998-2000 regarding testing of sensitive items like GMR heads for disk drives.
Do I need to take any ESD precautions when I service or repair products in the field?
If you’re servicing ESD sensitive products in the field, you need to take the same ESD control precautions that you would take in the manufacturing environment. This includes using wrist straps, protective work surfaces, and even placing products in protective packaging. These items should be part of your ESD field service kit. The challenge that you face in field service is that you are working in someone else’s environment, one over which you have little control. You may face low relative humidity, or an office with static generating carpet, or a lack of work space. Your customer may not know whether the products you work on are ESD sensitive or not. You need to be adaptable to the environments in which you are working. For example, in addition to your wrist strap, carry extra alligator clips, jacks, and extension cords. You should assume that all the products you work on are ESD sensitive and handle them accordingly. Take the extra time to clear a work area large enough to place your protective work surface. Follow good ESD protection procedures at all times. Your responsibility is to help solve your customers’ problems, not contribute to them.
How can I choose the best ESD ionizer, and how should I verify them?
A charge plate monitor can be used to verify that an ionizer is in proper working order. A charge pate works like this: An electrical potential is applied to a metal plate of fixed size and capacitance. A non-contacting voltmeter reads the applied potential. A timer measures the time it takes an ionizer to neutralize the plate potential usually from 10
00 volts to less than 100 volts. Other ranges can be established depending on the application. The test methods most often used are available from the ESD Association at www.esda.org.
Another important test for ionizers is to determine the balance of the ionization process. It is optimal if an ionizer produces and delivers a near equal amount of positive and negative air ions. If an ionizer is off-balance, it can actually charge a surface. The balance is measured using the same equipment described above, only in a slightly different mode. Most ionizers today are fairly stable in performance. They should be verified for performance probably quarterly or twice a year depending on your program requirements. For more information on testing ionizers and application of ionizers, contact the ESD Association as mentioned above. There is a Standard ANSI/ESD S20.20 and other information that could assist you for nominal dollars.
Transforming Technologies offers ESD Consulting Services through LBL Scientific. LBL Scientific can guide you to a more profitable factory by elliminating the sources of ESD damage, mitigating microcontamination issues and identifying EMI from ESD that is effecting your robotics and automated test systems.
Some static generative items (i.e., monitors, key boards or special items) must be used in a static controlled area, how do you provide static protection under these circumstances?
Ideally, we should try to keep these static generating materials to a minimum in any ESD-protective environment. However, this is not always possible. If you have to use them, there are several steps you can take to reduce their possible impact on your ESD-sensitive products. First, keep the static generators as far away from your ESDS products as possible, preferably several feet. Second, be sure to keep ESDS products from entering any field that may be produced by the static generator. Third, if the static generator is a conductor, ground it if possible to remove any charge that may be generated on it. Fourth, treat the surface of the static generator with a topical antistat to reduce the charge generated on the material. Fifth, ionize the material to remove any generated charges. Sixth, if the charge generator is employee clothing, use static protective garments to help suppress any fields from the clothing. You may need to implement several of these steps to provide adequate static protection.